Maritime 3D Printing Revolutionized: Hyundai-ABS's Onboard Printer Leads the Way
Rewritten Article:
Shipping disasters on the open sea can lead to expensive repairs and lengthy delays. The ability to manufacture parts onboard could mean the difference between a minor setback and a major operational failure. Additive manufacturing (AM), long celebrated for its game-changing potential in industries like aerospace and healthcare, is finally making waves in the maritime sector with recent advancements by HD Hyundai Heavy Industries (HHI).
With numerous challenges specific to shipbuilding and the unpredictable nature of the sea, maritime applications of AM have been growing at a slower pace compared to other industries. But HHI's latest breakthrough could tip the scale. Their containerized "3D Printing Digital Workshop"—a collaboration with the American Bureau of Shipping (ABS), Ulsan metro City, CS CAM, and KITECH—represents the bleeding edge of 3D printing in the maritime industry.
Maritime 3D Printing Today
Over the past decade, the maritime 3D printing sector has been maturing, albeit slowly. Shipping giant Wilhelmsen, for instance, has led the charge in delivering spare parts to seagoing vessels using AM. Even going so far as partnering with German engineering leader thyssenkrupp to establish a joint venture called Pelagus 3D, dedicated to 3D printing for maritime and beyond.
Meanwhile, standards bodies such as the American Bureau of Shipping (ABS) have been conducting research to establish guidelines and validate numerous 3D printed parts for marine customers.
"AM has been gaining ground over the past decade, with recent years seeing an acceleration in progress," said Dr. Gu Hai, Vice President of Technology at ABS. "As industries are embracing digitization, decarbonization, and supply chain resilience, this is the ideal time for the maritime sector to adopt this technology. ABS is ready to support this transition as the global leader in classification services for marine and offshore assets."
The Future of Maritime 3D Printing
All navies across the globe have invested in 3D printing technology, with the United States Navy being the most dedicated so far, boasting onboard metal 3D printers like those found on the USS Essex. However, the latest announcement from HHI represents a watershed moment for maritime AM. HHI's ambitious project, supported by the Korean government, to develop an all-encompassing AM unit for deployment on vessels has culminated in the world's first commercial vessel equipped with onboard metal AM capabilities—the 3D Printing Digital Workshop.
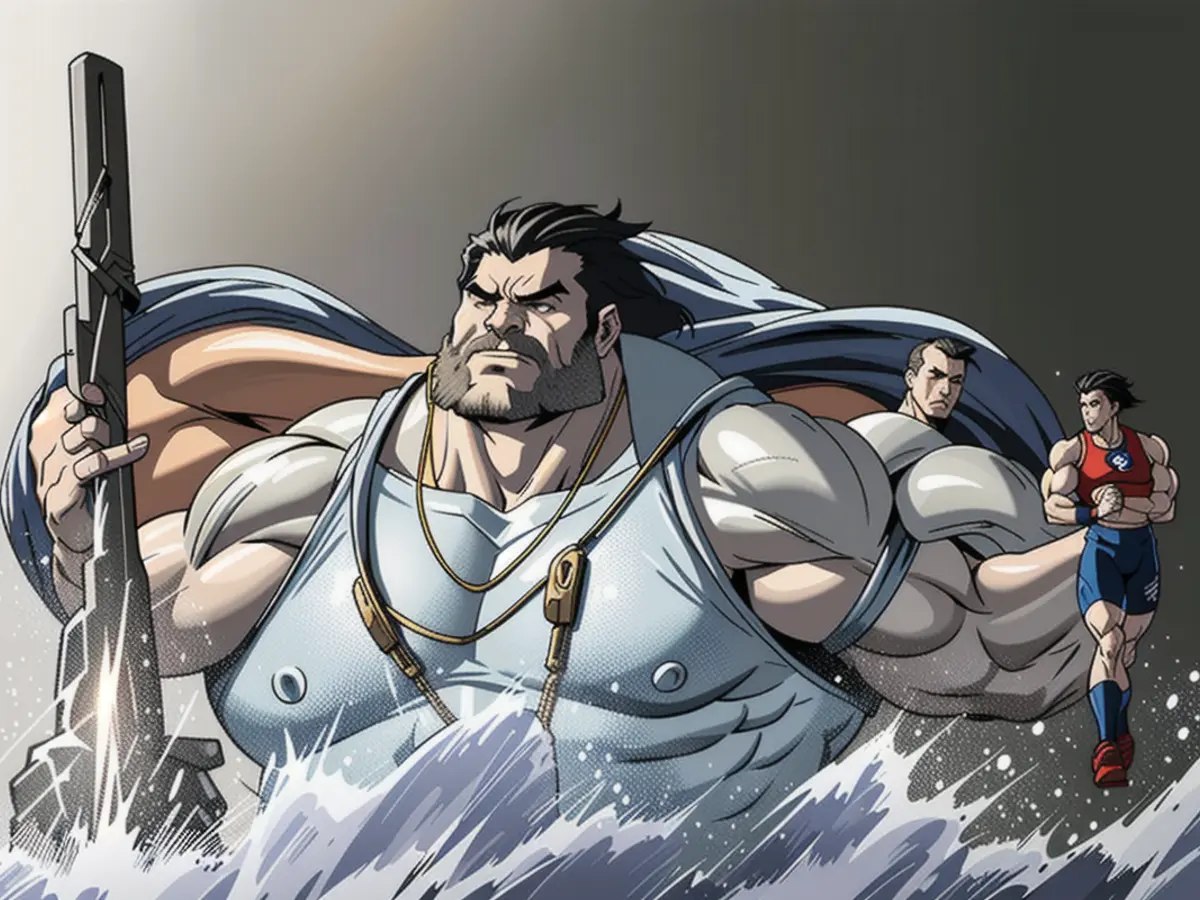
HHI's innovation incorporates a motion compensation system designed to counteract the rocking of a ship, and a humidity control system to maintain printing quality on par with land-based facilities. This game-changing setup has already been triumphantly tested during sea trials with the successful production of components onboard despite the vessel's movement.
Benefits and Implications
One primary advantage of this technology is the drastic reduction in lead times for critical spare parts. HHI estimates that their system could cut down on the 233-day average wait for replacement components to just two days. Such time savings could significantly reduce vessel downtime and the logistical costs associated with transporting replacement parts from the shore.
Moreover, HHI is developing metal powders specifically designed for shipbuilding applications. The company's new powder, called SS400 in the maritime industry, is significantly cheaper than current market powders, making it a viable option for widespread adoption.
Gearing Up for a Maritime Digital Supply Chain
HHI intends to roll out both the onboard 3D printing system and the new carbon-steel material commercially. They envision a future where 3D printing is integrated into a digital supply chain for ship maintenance and repair. The goal is to establish digital libraries of essential components, allowing ships to order parts online and have them printed at nearby ports or onboard, reducing the reliance on traditional supply chains.
With its continuous support of cutting-edge research and industry partnerships, ABS is paving the way for the adoption of 3D printing in the maritime sector. As this technology becomes more prevalent in maritime operations, shipbuilders and operators alike will need to adapt to the shifting landscape. The interconnected network of 3D printing hubs may well usher in a new era for shipbuilding and maintenance.
- The containerized "3D Printing Digital Workshop" by Hyundai Heavy Industries (HHI), in collaboration with ABS, is probably a game-changer in the maritime industry, propelling the viability of additive manufacturing in shipbuilding.
- HHI's new metal powder, SS400, has been developed specifically for shipbuilding applications and could potentially revolutionize the maritime 3D printing sector due to its low cost, making it a viable option for widespread adoption.
- The integration of 3D printing into a digital supply chain for ship maintenance and repair, as envisioned by HHI, could probably lead to significant reductions in vessel downtime and logistical costs, thanks to on-demand printing of critical spare parts at sea or nearby ports.